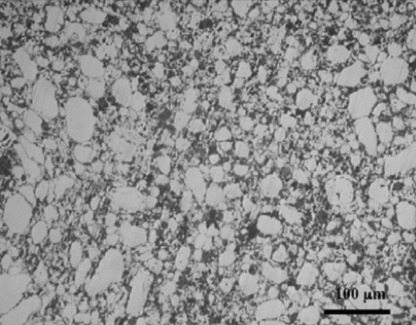
بررسی اثر ذرات مس وآلومینا بر ویژگیهای کامپوزیت Cu-Al2O3
در این مطالعه به بررسی ویژگیهای کامپوزیت Cu-Al2O3 پرداخته شده است. کامپوزیتهای بر پایه مس، از استحکام و پایداری حرارتی مناسبی برخوردار هستند که آنها را برای استفاده در الکترودهای جوشکاری مقاومتی، قابهای پایه، شتابدهندهها و اتصالدهندههای الکتریکی مناسب میسازد. برای بهدستآوردن یک کامپوزیت عالی، نیاز به ذرات تقویتکننده اکسید در زمینه مس با توزیع همگن است.
برای بهدستآوردن یک کامپوزیت عالی، نیاز به توزیع همگن و اندازه کوچک ذرات اکسید در زمینه مس است. روش مرسوم برای تولید پودر کامپوزیت اکسید فلز، روش اکسیداسیون داخلی است. یکی از عیوب اصلی اکسیداسیون داخلی، توزیع ناهمگن ذرات اکسید است که بر خصوصیات مکانیکی و الکتریکی کامپوزیتهای اکسید فلزی تأثیر منفی میگذارد. روشهای آلیاژسازی مکانیکی و انجماد سریع برای حل این مشکل پیشنهاد شده است. با این حال، به گفته برخی از نویسندگان، فرآیند اکسیداسیون داخلی موفقترین و تکرارپذیرترین روش ساخت این دسته از کامپوزیتها است.
بر اساس تحقیقات گذشته، کامپوزیتهای تقویتشده با اکسید فلز مانند کامپوزیت Cu-Al2O3، حتی پس از قرارگیری در دمای نزدیک به نقطه ذوب مس، به دلیل وجود ذرات تقویتکننده پایدار که مانع از حرکت مرزدانهها میشوند، مقاومت بسیار خوبی را در برابر نرمشدن از خود نشان میدهند.
در این مطالعه، به منظور تولید کامپوزیت Cu-Al2O3 از آسیابکاری با انرژی بالا استفاده شده است. پودر مس پیشآلیاژی اتمیزهشده با گاز خنثی با متوسط اندازه ذرات 30 میکرومتر حاوی 2 درصد وزنی Al(Cu-2wt.%Al) و مخلوط پودرهای مس الکترولیتی با متوسط اندازه ذرات 30 و 15 میکرومتر به همراه 4 درصد وزنی پودر تجاری اکسید آلومینیوم Al2O3 (Cu*-4wt.% Al2O3 و Cu-4wt.%Al) به عنوان مواد اولیه استفاده شدهاند. آسیابکاری پودرهای مس پیش آلیاژشده توسط اکسیداسیون داخلی با اکسیژن هوا، باعث تشکیل ذرات Al2O3 در اندازه نانو شده است. پودر کامپوزیت بهدستآمده پس از 5 و 20 ساعت آسیابکاری، تحت پرس گرم قرار گرفته و سپس به مدت 1 و 5 ساعت در معرض دمای بالا در گاز آرگون در دمای 800 درجه سانتیگراد قرار گرفتند.
اعوجاج شبکه پودرهای کامپوزیت Cu-Al2O3
شکل زیر اعوجاج شبکه پودرهای کامپوزیت Cu-Al2O3 را نشان میدهد. اعوجاج شبکه در پودر کامپوزیت Cu-2wt.%Al تقویتشده با ذرات بسیار کوچک Al2O3 با افزایش زمان آسیاب افزایش مییابد، در حالی که کمترین اعوجاج شبکه ممکن است در مخلوط پودر Cu *-4wt.% Al2O3 دیده شود. مطابق شکل زیر، زمانی که اندازه ذرات پودرهای مس اولیه کوچکتر باشد، اعوجاج شبکه کاهش مییابد.
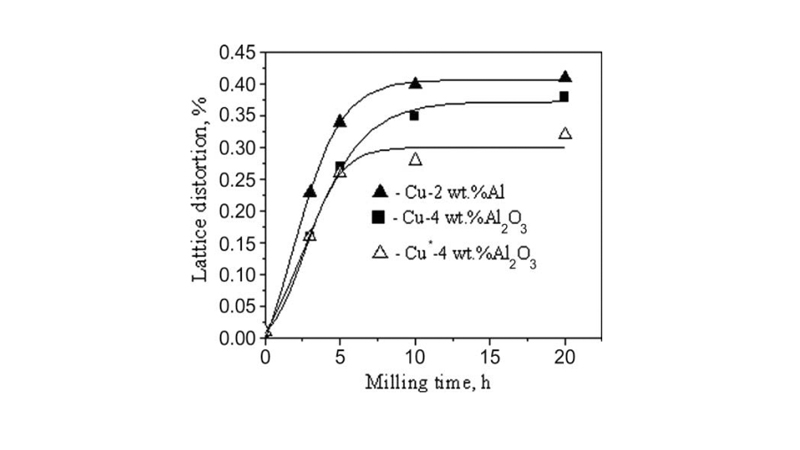
اثر زمان آسیابکاری روی اعوجاج شبکه پودرهای کامپوزیت Cu-Al2O3.
وجود ذرات Al2O3 در اندازه نانو، باعث افزایش اعوجاج شبکه میشود، یعنی ذرات Al2O3 بسیار کوچک (100 نانومتر) باعث ایجاد اعوجاج شبکه بیشتری نسبت به ذرات درشت (75/0 میکرومتر) میشوند.
مورفولوژی و ساختار پودرهای کامپوزیت Cu-Al2O3
شکل زیر، میکروگرافهای SEM مورفولوژی پودرهای کامپوزیت Cu-Al2O3 را پس از 3 ساعت و 20 ساعت آسیابکاری نشان میدهد. واضح است که پودرهای کامپوزیت بر پایه پودر و مخلوطهای پیشآلیاژی، اندازه و مورفولوژی متفاوتی پس از 3 ساعت آسیابکاری دارند (شکلهای الف – ج). پودرهای کامپوزیت Cu-2wt.% Al (شکل الف) مسطح هستند، در حالی که پودرهای کامپوزیت Cu-4wt.% Al2O3 و Cu*-4wt.% Al2O3 گردتر هستند (شکلهای ب و ج به ترتیب).
علاوه بر این، پودرهای کامپوزیت Cu-4wt.% Al2O3 از نظر اندازه بسیار متفاوت هستند. شکل مسطح پودرهای کامپوزیت Cu-2wt.% Al به دلیل وجود نانوذرات Al2O3 ناشی از اکسیداسیون داخلی است که مقاومت بالاتری نسبت به میکروذرات Al2O3 تجاری در ابتدای آسیابکاری در برابر تغییر شکل پلاستیک قوی ایجاد میکنند.
در طول آسیابکاری طولانی مدت 20 ساعته (شکلهای د – و)، اندازه پودرهای کامپوزیت Cu-2wt.% Al (شکل د) بهطور قابلتوجهی کاهش مییابد و ذرات گردتر میشوند. از طرف دیگر، پودرهای کامپوزیت Cu-4 wt.% Al2O3 نیز دارای مورفولوژی مشابه است و افزایش اندازه ذرات مشاهده شد (شکل ه). به دلیل عدم تعادل فرآیندهای شکستگی و جوشکاری ذرات پودر در طول 20 ساعت آسیابکاری، پودر کامپوزیت Cu-2wt.%Al و Cu-4wt.%Al2O3 دارای اندازه یکنواختی نیستند.
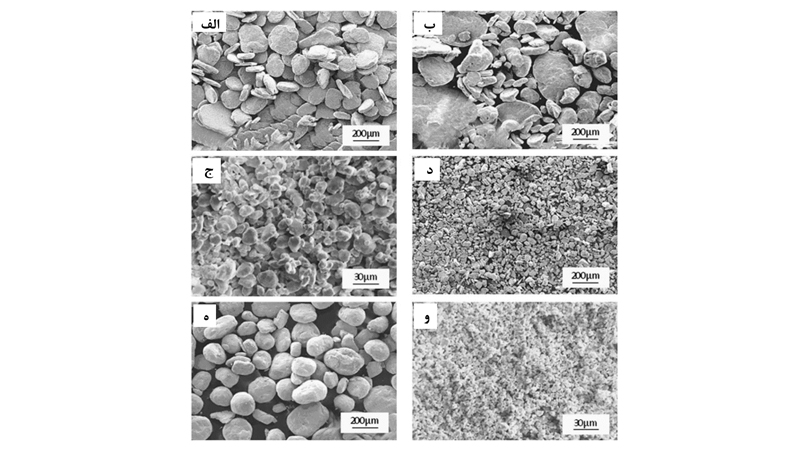
مورفولوژی پودرهای کامپوزیت Cu-Al2O3. پودرهای Cu-2wt.%Al، Cu-4wt.%Al2O3 و Cu*-4wt.%Al2O3(الف – ج) پس از 3 ساعت و (د – و) بعد از 20 ساعت آسیابکاری.
بر اساس نتایج SEM پودرهای کامپوزیت Cu-Al2O3، اندازه ذرات مس اولیه و همچنین اندازه ذرات Al2O3 بر مورفولوژی و اندازه ذرات پودرهای کامپوزیت در طول آسیابکاری تأثیر میگذارند.
شکل زیر (الف – د)، ریزساختار پودرهای کامپوزیت Cu-Al2O3 را پس از 20 ساعت آسیابکاری نشان میدهد. پودرهای کامپوزیت آسیابشده، دارای ساختار لایهای هستند. لایهها، نمایانگر مس پیشآلیاژی اولیه با تغییر شکل پلاستیک (شکل الف) و ذرات پودر مس (شکل ب) هستند. در ساختار Cu*-4 wt.% Al2O3، لایههای پودر کامپوزیت به دلیل اندازه ذرات پودر بسیار کوچک قابل مشاهده نیستند (شکل ج). اعمال ساختار لایهای بسیار ظریف با بزرگنمایی بالاتر را میتوان در پودر کامپوزیت Cu*–4 wt.% Al2O3 تشخیص داد (شکل د).
تصاویر میکروسکوپ نوری پودرهای کامپوزیت Cu-Al2O3 پس از 20 ساعت آسیابکاری. (الف – ج) پودرهای کامپوزیت Cu–2 wt.%Al; Cu–4 wt.% Al2O3; Cu*–4 wt.% Al2O3. (د) میکروساختار SEM پودر کامپوزیت Cu*–4 wt.% Al2O3.
مطابق شکل زیر، کامپوزیتها ساختار لایهای پودرهای کامپوزیت آسیابکاریشده در شکل بالا را حفظ کردند. لایهها در کامپوزیت Cu*-4 wt.% Al2O3 (شکل ج) در مقایسه با کامپوزیتهای Cu-2 wt.% Al و Cu-4 wt.% Al2O3 (به ترتیب شکلهای الف و ب)، بسیار ظریفتر است. نواحی که با فلش در ریزساختار کامپوزیتهای Cu-2wt.%Al، Cu-4wt.% Al2O3 و Cu*-4wt.% Al2O3 مشخص شدهاند نشاندهنده تبلور مجدد در حین پرس گرم است.
تبلور مجدد در کامپوزیت Cu-2 wt.% Al در گوشههای پودرهای کامپوزیت آسیابشده قبلی رخ داده است که در آن تنش غلظت اعمالشده در طول پرس بالاترین مقدار است. در کامپوزیتهای Cu-4 wt.% Al2O3 و Cu*-4 wt.% Al2O3 نواحی تبلور مجدد، پودرهای آسیابشده را در ابعاد مختلف احاطه کردهاند. تغییرات ریزساختاری کامپوزیتها و همچنین موقعیت و میزان تبلور مجدد نتیجه اندازه متفاوت ذرات مس اولیه است.
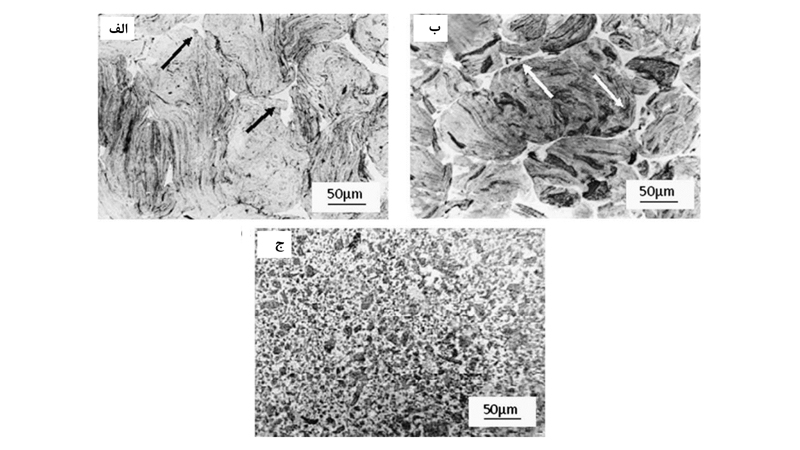
تصاویر میکروسکوپ نوری پودرهای کامپوزیت Cu-Al2O3. (الف – ج) کامپوزیتهای
Cu–2 wt.%Al; Cu–4 wt.% Al2O3; Cu*–4 wt.% Al2O3 به ترتیب.
میکروسختی و پایداری حرارتی پودرهای کامپوزیت Cu-Al2O3
تاثیر زمان آسیابکاری بر میکروسختی پودرهای کامپوزیت Cu-Al2O3 در شکل زیر نشان داده شده است. میکروسختی کامپوزیتها با افزایش زمان آسیابکاری افزایش مییابد. میکروسختی کامپوزیتهای Cu-4wt.% Al2O3 و Cu*-4wt.% Al2O3 بهطور مداوم با افزایش زمان آسیابکاری افزایش مییابد، بهطوری که بزرگترین افزایش میکروسختی کامپوزیت Cu-2wt.%Al در طول 5 ساعت اول آسیابکاری رخ داده و آسیابکاری بیشتر منجر به تغییر ناچیز در میکروسختی این کامپوزیت شده است. حداکثر مقادیر میکروسختی کامپوزیتهای Cu*–4 wt.% Al2O3 ; Cu–4 wt.% Al2O3 ; Cu–2 wt.%Al ناشی از 20 ساعت آسیابکاری، به ترتیب 2350، 1730 و 1790 مگاپاسکال است.
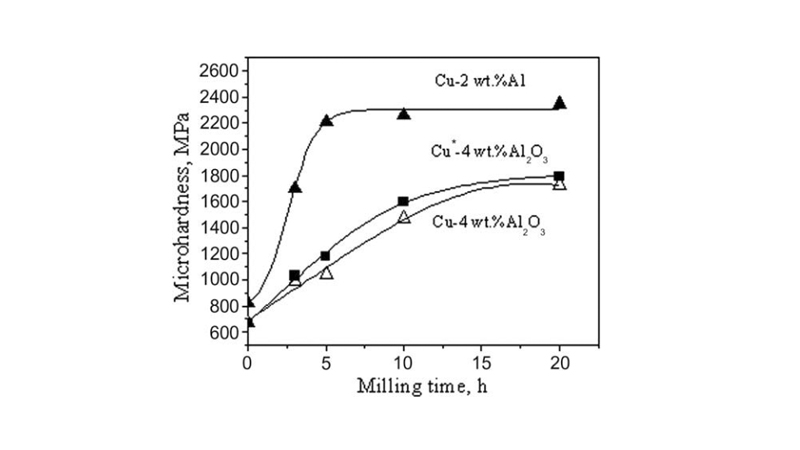
اثر زمان آسیابکاری روی میکروسختی پودرهای کامپوزیت Cu-Al2O3.
مقدار میکروسختی کامپوزیت Cu-2wt.% Al بیشتر از میکروسختی سایر پودرهای کامپوزیت Cu-Al2O3 است که این امر به دلیل تقویتکنندگی قویتر نانوذرات Al2O3 در زمینه مس، نسبت به میکروذرات Al2O3 است. تفاوت در میکروسختی کامپوزیتهای Cu-4wt.%Al2O3 و Cu*-4wt.%Al2O3، ناشی از تفاوت در اندازه کریستالیت پودرهای کامپوزیت آسیابشده پرسشده است.