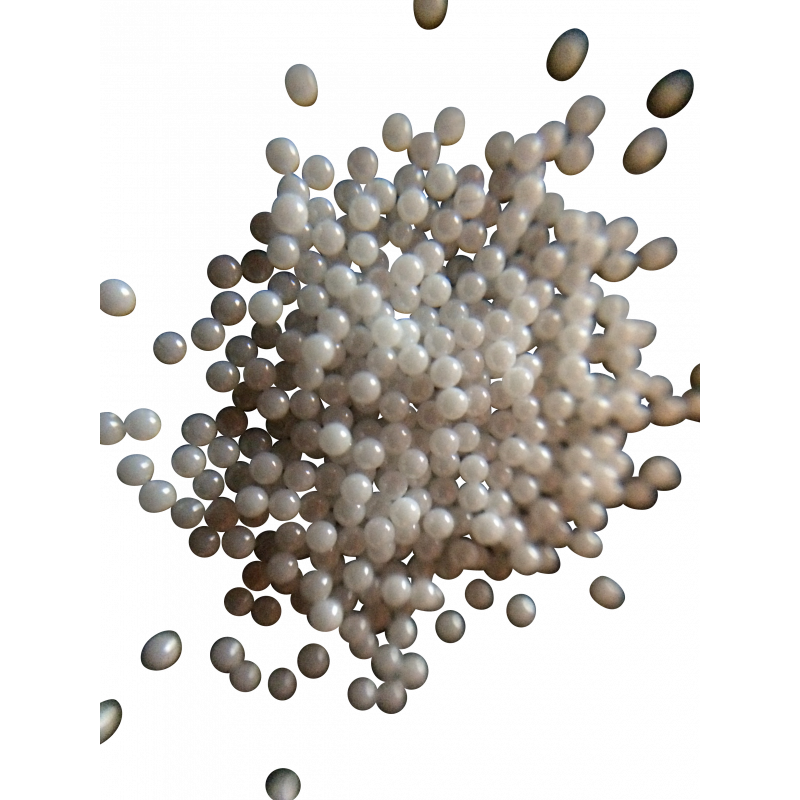
تولید پودر زیرکونیای پایدارشده با ایتریا به روش آلیاژسازی مکانیکی
زیرکونیای پایدارشده با ایتریا (YSZ)، یکی از سرامیکهای با کارایی بالا است که از خواصی چون سختی بالا، رسانایی حرارتی کم، چقرمگی بالا، رسانایی یونی عالی و همچنین مقاومت در برابر سایش، خوردگی و تشعشع بالا برخوردار است. آلیاژسازی مکانیکی (MA)، یک تکنیک پردازش پودر حالت جامد است که در آن ذرات در معرض جوش سرد مکرر، شکستگی و جوشکاری مجدد در آسیاب گلولهای با انرژی بالا قرار میگیرند. MA از لحاظ تاریخی، یکی از موثرترین روشها برای تولید طیف وسیعی از مواد سرامیکی بوده و در حال حاضر نیز هست. پودر YSZ میتواند بهطور موثر توسط MA از ZrO2 با مقدار مورد نیاز Y2O3 بر اساس فاز مورد نظر تولید شود. در این مطالعه به بررسی تولید پودر زیرکونیای پایدارشده با ایتریا (YSZ) به روش آلیاژسازی مکانیکی میپردازیم.
در تحقیقی که توسط الدسوکی و همکارانش در سال 2022 در دانشگاه الازهر مصر انجام گرفت، زیرکونیا با خلوص بالا (62/99 درصد) با موفقیت از زیرکون مصر سنتز شده و متعاقبا با 10 درصد مولی ایتریا از طریق آلیاژسازی مکانیکی بهطور کامل پایدار شده و اثر زمان آسیابکاری بر روی سنتز پودر زیرکونیای پایدارشده با ایتریا مورد بررسی قرار گرفته است. آلیاژسازی مکانیکی در آسیاب گلولهای سیارهای از جنس فولاد زنگنزن با سرعت چرخش 350 دور در دقیقه و نسبت وزن توپ به پودر 10 انجام شده است. این آسیاب از یک دیسک چرخشی با دو کاسه تشکیل شده است. دیسک در یک جهت میچرخد در حالی که کاسهها برعکس میچرخند، که این امر باعث ایجاد نیروهای گریز از مرکز میشود که در جهت مخالف عمل میکنند. درنتیجه، محیط آسیاب و پودرهای باردار بهطور متناوب روی دیواره داخلی محفظه آسیاب میچرخند و مطابق شکل1 با سرعت بالا در کاسه پرتاب میشوند.
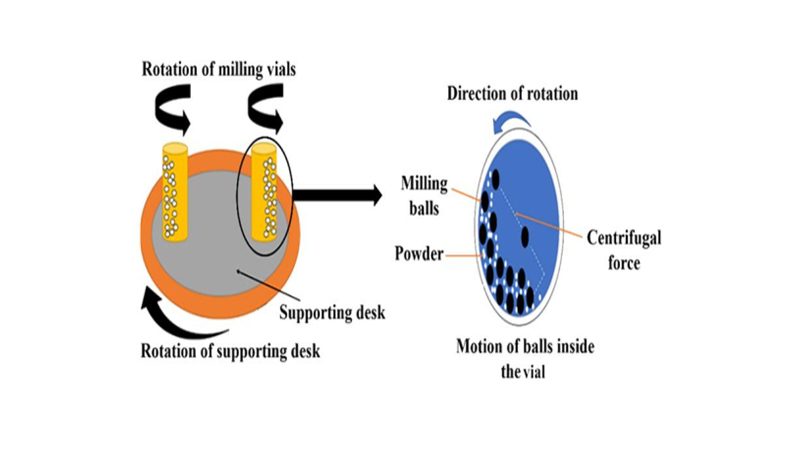
شکل1. مکانیزم آسیابکاری پودر در آسیاب گلولهای.
اثر زمان آسیابکاری و نسبت گلوله به پودر در سنتز پودر زیرکونیای پایدارشده با ایتریا
الگوهای XRD پودرهای آسیابشده زیرکونیای پایدارشده با ایتریا برای 8، 16، 24 و 32 ساعت در شکل2 نشان داده شده است. هنگام مقایسه الگوهای ZrO2 آسیابشده دیگر با الگوی 8 ساعت، مشاهده میشود که پهنای پیکها بهطور قابلتوجهی افزایش یافته و شدت پیکهای قوی m-ZrO2 کاهش یافته است. این امر به دلیل کاهش اندازه دانه و افزایش میکروکرنشها طی فرآیند آسیابکاری است. کاهش اندازه کریستالیت، واکنش شیمیایی و انرژی سطحی پودر را افزایش میدهد. همچنین، عیوب کریستالی و اختلال ساختاری، به نفوذ یونهای Y3+ در شبکه m-ZrO2 و بازآراییهای اتمی کمک میکند. همه این عوامل منجر به پایداری فاز مکعبی در دمای بالا شده که با پیکهای جدید تشکیلشده در مقادیر θ2( ˚30، ˚7/34، ˚50 و ˚9/59) و همچنین عدم وجود پیکهای c-Y2O3 نشان داده میشود. همه این یافتهها به این معنی است که MA بهخوبی پیش رفته است. ساختارهای زیرکونیایی تتراگونال و مکعبی بسیار شبیه به هم هستند که شناسایی هر فاز را بسیار دشوار میکند. بنابراین، پیکهای جدید با SZ (زیرکونیای پایدارشده) مشخص شدهاند. همانطور که الگوی پراش نمونه آسیابشده به مدت 8 ساعت نشان داد، MA منجر به افزایش پهنای پیک شده که تفسیر و محاسبات بعدی را دشوارتر میکند. بنابراین، برای زمانهای آسیابکاری طولانیتر در 16، 24 و 32 ساعت، نمونهها به مدت 3 ساعت در دمای 800 درجه سانتیگراد آنیل شدند تا بلورینگی افزایش و پیکها واضحتر شوند و تفسیر و محاسبات آسانتر انجام شود.
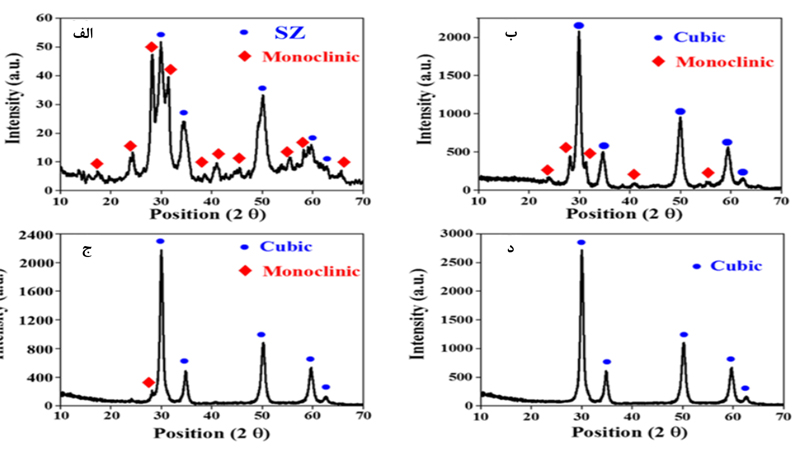
شکل2. الگوهای XRD نمونههای پودر آسیابشده زیرکونیای پایدارشده با ایتریا ، الف) 8 ساعت، ب) 16 ساعت، ج) 24 ساعت، د) 32 ساعت.
با افزایش زمان به 16 ساعت، نسبت زیرکونیای پایدارشده با ایتریا بهتدریج با کاهش m-ZrO2 افزایش یافته و به فاز غالب تبدیل میشود. بر اثر عملیات حرارتی، پیکها نسبت به آسیابکاری 8 ساعته، شدیدتر و تیزتر هستند. SZ دارای ساختار مکعبی است. افزایش بیشتر زمان آسیابکاری به 24 ساعت، منجر به ناپدیدشدن پیکهای m-ZrO2 شده و پس از 32 ساعت، ساختار بهطور کامل به c-ZrO2 تبدیل شده است.
تصاویر SEM پودرهای آسیابشده زیرکونیای پایدارشده با ایتریا در شکل3 نشان داده شده است. همه نمونهها از ذرات بسیار ریز مجزا و آگلومرههای نسبتا بزرگ تشکیل شدهاند. با رسیدن زمان آسیابکاری به 32 ساعت نسبت به نمونه 8 ساعته، اندازه کریستالیت حدود ده برابر کاهش یافته و مقادیر میکروکرنشها نسبتا یکسان است، زیرا عملیات حرارتی تمام میکروکرنشهای پودرهای آسیابشده را حذف کرده است.
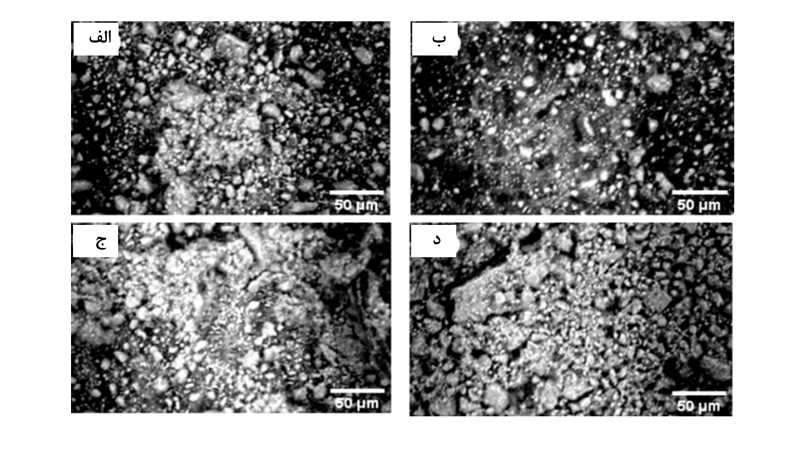
شکل3. میکروگرافهای SEM نمونههای پودر آسیابشده زیرکونیای پایدارشده با ایتریا، الف) 8 ساعت، ب) 16 ساعت، ج) 24 ساعت، د) 32 ساعت.
در تحقیقی دیگر، گوانگدی ژو و همکارانش در سال 2019 در چین، به بررسی اثرات زمان آسیابکاری (tm)، نسبت جرمی گلوله به پودر (BPMRs)، دما و زمان کلسیناسیون و نسبت زیرکونیا به ایتریا در سنتز پودر زیرکونیای پایدارشده با ایتریا پرداختند. بدین منظور، زیرکونیای مونوکلینیک بهصورت مکانیکی با ایتریا (14-6 درصد مولی) به وسیله آسیاب گلولهای در نسبتهای جرمی مختلف گلوله به پودر به مدت 24-3 ساعت آلیاژ شده و سپس پودرهای آسیابشده در 1100 درجه سانتیگراد و 1500 درجه سانتیگراد به مدت 10-2 ساعت کلسینه شدند.
شکل4 الگوهای پراش پرتو ایکس نمونههای آسیابشده طی زمانهای مختلف را نشان میدهد. همانطور که مشاهده میشود، پدیده همپوشانی پودرها در محدوده 32-28 درجه رخ داده است. با افزایش زمان آسیابکاری، شدت پراش m-ZrO2 کاهش و درجه آمورفیزاسیون بهطور مداوم افزایش یافته است. علاوه بر این، این الگو دارای یک پیک در حدود 2/29 درجه است که مربوط به (222) Y2O3 است که نشان میدهد مقداری پودر ایتریا هنوز در مرحله اولیه فرآیند یعنی زیر 8 ساعت، دارای ساختار مکعبی (bcc) است. هنگامی که زمان آسیابکاری از 8 ساعت بیشتر شده است، پیکهای پراش Y2O3 ناپدید شده و پیک (111) مربوط به تشکیل پودر زیرکونیای پایدارشده با ایتریا در 9/29 درجه مشاهده میشود، به این معنی که در طول فرآیند آلیاژسازی مکانیکی، پودر تحت انتقال فاز قرار گرفته است.
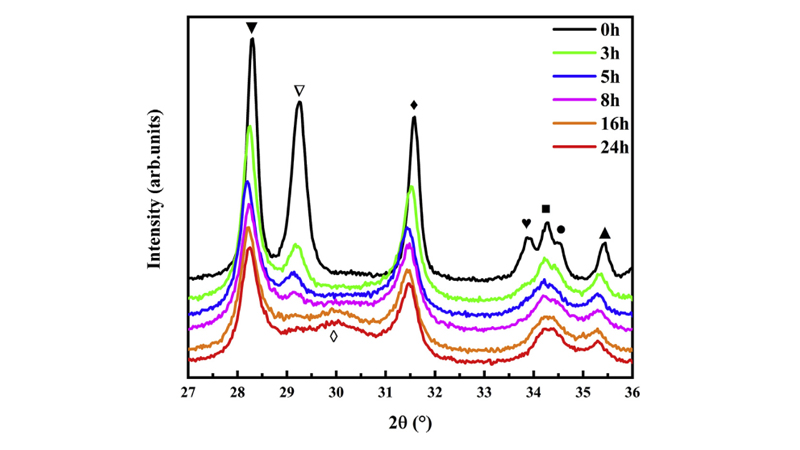
شکل4. الگوهای پراش پرتو ایکس پودرهای مخلوطشده (مقدار Y2O3 اولیه 7/10 درصد مولی) پس از آلیاژسازی مکانیکی طی بازه زمانی 24-0 ساعت و شکلگیری پودر زیرکونیای پایدارشده با ایتریا. (▼) (111-) ZrO2، (∇) (222) Y2O3، (◊) (111) c-YSZ، (♦) (111) ZrO2، (♥) (400) Y2O3، (■) (200) ZrO2، (●) (020) ZrO2 و (▲) (002) ZrO2. در زمان 0 ساعت، پودر فقط مخلوط شده است.
با افزایش نسبت جرم گلوله به پودر (BPMRs) نیز، شدت پیک پراش مربوط به پودر زیرکونیای پایدارشده با ایتریا افزایش متناظری را نشان میدهد که حاکی از افزایش مقدار YSZ است. واضح است که افزایش نسبت جرم گلوله به پودر، میتواند احتمال برخورد پودر و گلوله را بهبود بخشد.
اثر دما و زمان کلسیناسیون در سنتز پودر زیرکونیای پایدارشده با ایتریا
نمودار زیرکونیای آزاد در مقابل زمان آسیابکاری در شکل 5ب، نشان داده شده است. در مراحل اولیه فرآیند آسیابکاری، کاهش شدیدی در مقدار m-ZrO2 وجود دارد. هنگامی که زمان بیشتر از 8 ساعت شده، Y2O3 از قبل در پودر ZrO2 پراکنده شده است. پس از آن، انتشار Y3+ توسط عیوب و فواصل نفوذی کوتاه ناشی از آلیاژسازی مکانیکی تقویت شده است. با این حال، راندمان آسیاب بهتدریج در طول زمان کاهش یافته است. هنگامی که زمان از 16 ساعت بیشتر شده، مقدار m-ZrO2 آزاد بهطور گسترده (12 درصد وزنی) باقیمانده که به این معنی است که ساختاری ناپایدار تشکیل شده است. بنابراین توزیع یکنواخت دیگر نمیتواند از نظر فیزیکی با آلیاژسازی مکانیکی بهبود یابد. بدیهی است که یک گرادیان غلظتی نسبتا بزرگی از یونهایY3+ در پودر مخلوطشده بر پایه زیرکونیا وجود دارد. علاوه بر این، با توجه به مطالعه رفتار نفوذ عناصر در کریستالهای زیرکونیای پایدارشده با ایتریا، ضریب خودنفوذی کاتیونی (Ds) با افزایش مقدار Y3+ ترکیب YSZ کاهش مییابد. بنابراین، یونهای Y3+ باید بهراحتی در اکسید زیرکونیوم در دمای بالا برای پودر مخلوطنشده نفوذ یابند. با این حال، بهطور کلی، انرژی فعالسازی نفوذ اتمهای Y دارای مقدار بیشتری (کمتر از) است، زیرا اتمهای ایتریم به عنوان اتمهای جایگزین وارد شبکه بلوری زیرکونیا میشوند. از این رو، پس از کلسیناسیون در دمای 1100 درجه سانتیگراد به مدت 2 ساعت، تنها مقادیر کمی از زیرکونیا و ایتریا به زیرکونیای پایدارشده با ایتریا تبدیل میشوند (شکل5الف).
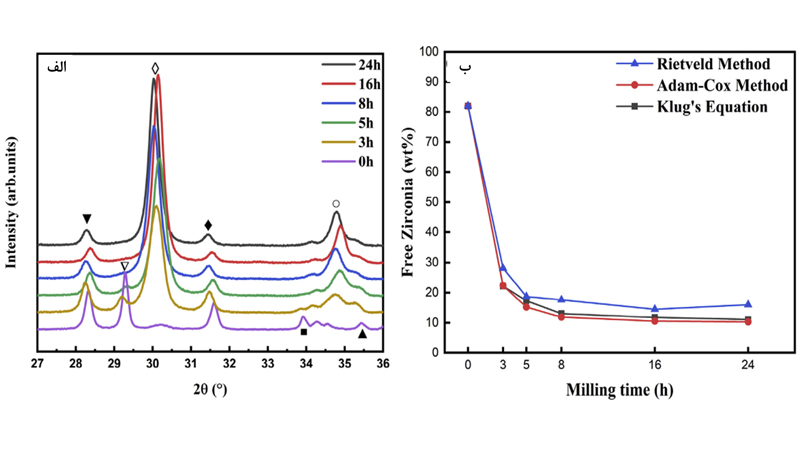
شکل5. الف) الگوهای پراش پرتو ایکس پودرهای مخلوطشده (مقدار Y2O3 اولیه 7/10 درصد مولی) پس از 24-0 ساعت آلیاژسازی مکانیکی و کلسیناسیون در دمای1100 درجه سانتیگراد به مدت 2 ساعت و شکلگیری پودر زیرکونیای پایدارشده با ایتریا. (▼) (111-) ZrO2، (∇) (222) Y2O3، (◊) (111) c-YSZ، (♦) (111) ZrO2، (■) (200) ZrO2، (●) (020) ZrO2 و (▲) (002) ZrO2. ب) نسبت زیرکونیا در پودر به روشهای مختلف محاسبه شده است. مقدار اولیه زیرکونیا (0=tm) برابر با 82 درصد وزنی است.
در مقابل، طی آسیابکاری پودر ایتریوم به دلیل شکستگی و جوش سرد، ایتریم بهطور مساوی در سراسر زمینه زیرکونیا توزیع میشود. از سوی دیگر، در طی فرآیند آسیابکاری، عیوب زیادی به دلیل شکستگی ایجاد میشود. بنابراین، نفوذ کاتیونها میتواند در دمای بسیار پایین رخ دهد. با این حال، بسیاری از عیوب ناپدید شده و تنش در فرآیند کلسیناسیون کاهش یافته و نفوذ دشوارتر میشود. بنابراین، پس از کلسیناسیون در دمای 1100 درجه سانتیگراد، ورود Y3+ به زیرکونیا در ترکیب زیرکونیای پایدارشده-ایتریوم، بسیار دشوار است. بر این اساس، مطابق شکل6الف، حتی اگر زمان کلسیناسیون طولانی شود، پیکهای پراش زیرکونیا (111–) و (111) همچنان وجود دارند و شدت آنها بهطور قابل ملاحظهای بدون تغییر باقی میماند.
هنگامی که دمای کلسیناسیون به 1500 درجه سانتیگراد افزایش مییابد، کاتیون دارای ضریب انتشار زیادی است. بنا بر تعریف کلی ضریب انتشار، بدون در نظر گرفتن تأثیر دما بر سایر پارامترها، Ds در 1500 درجه سانتیگراد 7 برابر بزرگتر از 1100 درجه سانتیگراد است. از این رو، مطابق شکل6ب، پس از کلسیناسیون پودر در دمای 1500 درجه سانتیگراد به مدت 4 ساعت، پیکهای پراش زیرکونیا در الگوی XRD بهطور کامل ناپدید شدهاند. علاوه بر این، هنگامی که زیرکونیای پایدارشده با ایتریا با 7/10درصد مولی Y2O3 اولیه (آسیابکاریشده به مدت 8 ساعت) در دمای 1500 درجه سانتیگراد در اکسیژن کلسینه میشود، جرم آن 67/12 درصد کاهش مییابد. این کاهش جرم به دلیل افزودن نایلون به عنوان کمکآسیاب است که از چسبیدن پودر به گلولهها و دیواره آسیاب جلوگیری میکند. این امر سبب کاهش نیروی محرکه آمورفیزاسیون و نرخ تبلور نیز میشود.
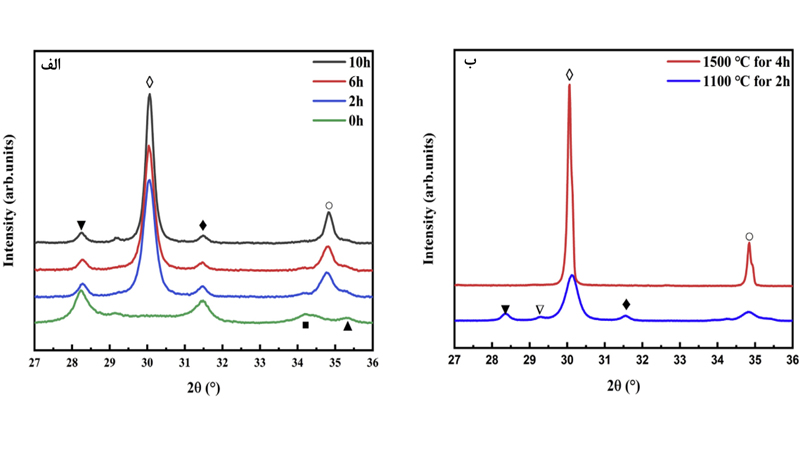
شکل6. الف) الگوهای پراش پرتو ایکس نمونههای پودر مخلوطشده (مقدار Y2O3 اولیه 7/10 درصد مولی) پس از آسیابکاری به مدت 8 ساعت و کلسیناسیون در دمای 1100 درجه سانتیگراد به مدت 2، 6 و 8 ساعت و شکلگیری پودر زیرکونیای پایدارشده با ایتریا. (▼) (111-) ZrO2، (◊) (111) c-YSZ، (♦) (111) ZrO2، (■) (200) ZrO2، (●) (020) ZrO2 و (▲) (002) ZrO2. ب) الگوهای پراش پرتو ایکس پودرهای مخلوطشده (مقدار Y2O3 اولیه 14 درصد مولی) پس از آسیابکاری به مدت 8 ساعت و کلسیناسیون در دمای 1100 و 1500 درجه سانتیگراد بهترتیب به مدت 2 و 4 ساعت. (▼) (111-) ZrO2، (∇) (222) Y2O3، (◊) (111) c-YSZ، (♦) (111) ZrO2، (○) (200) c-YSZ.
اثر مقادیر مختلف ایتریا در سنتز پودر زیرکونیای پایدارشده با ایتریا
مطابق شکل7، با افزایش مقدار اکسید ایتریم، شدت پیک پراش زیرکونیا همچنان کاهش مییابد (شکل 8)، که نشان میدهد افزودن فاز دوم میتواند برای شکستگی و نفوذ مفید باشد و راندمان آلیاژسازی مکانیکی را افزایش دهد. با این حال، هنگامی که مقدار اکسید ایتریم برابر با 12 درصد مولی است، مقدار زیرکونیای آزاد کمی افزایش مییابد. وقتی مقدار آن از حد معینی فراتر رود، کارایی دیگر افزایش یا حتی کاهش نخواهد یافت. علاوه بر این، مقداری اکسید ایتریم باقیمانده مشاهده میشود. با مطالعه کمی الگوهای XRD پودر زیرکونیای پایدارشده با ایتریا ، مشخص شد که مقدار باقیمانده زیرکونیا با مقدار ایتریا کاهش مییابد. با این حال، مقدار باقیمانده زیرکونیا درنهایت در یک محدوده مشخص در نوسان است. این ممکن است به تفاوت در خواص مکانیکی ایتریا و زیرکونیا مربوط باشد. هنگامی که محتوای ایتریا بالاتر باشد، عملکرد خود آن تأثیر خاصی بر کارایی آسیاب گلوله ای خواهد داشت.
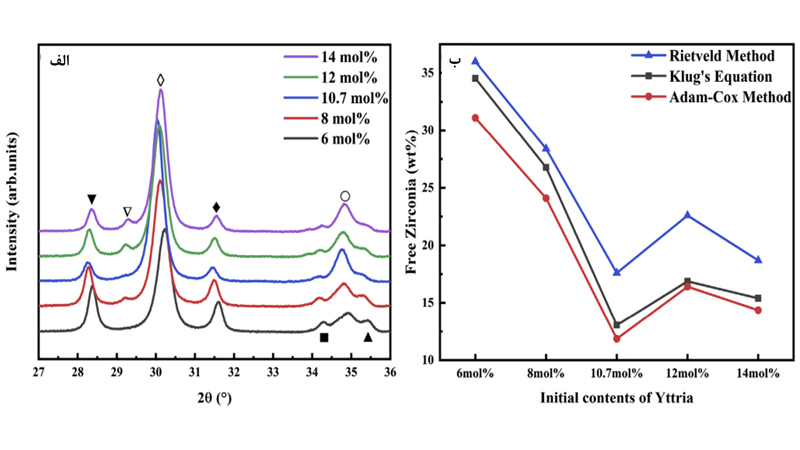
شکل7. الف) الگوهای پراش پرتو ایکس نمونههای پودر مخلوطشده شامل مقادیر مختلف از Y2O3 اولیه (6، 8، 7/10، 12 و 14 درصد مولی) پس از آسیابکاری به مدت 8 ساعت و کلسیناسیون در دمای 1100 درجه سانتیگراد به مدت 2 ساعت و شکلگیری پودر زیرکونیای پایدارشده با ایتریا. ب) تغییر در مقدار زیرکونیای آزاد به عنوان تابعی از ترکیب YSZ. (▼) (111-) ZrO2، (∇) (222) Y2O3، (◊) (111) c-YSZ، (♦) (111) ZrO2، (○) (200) c-YSZ.