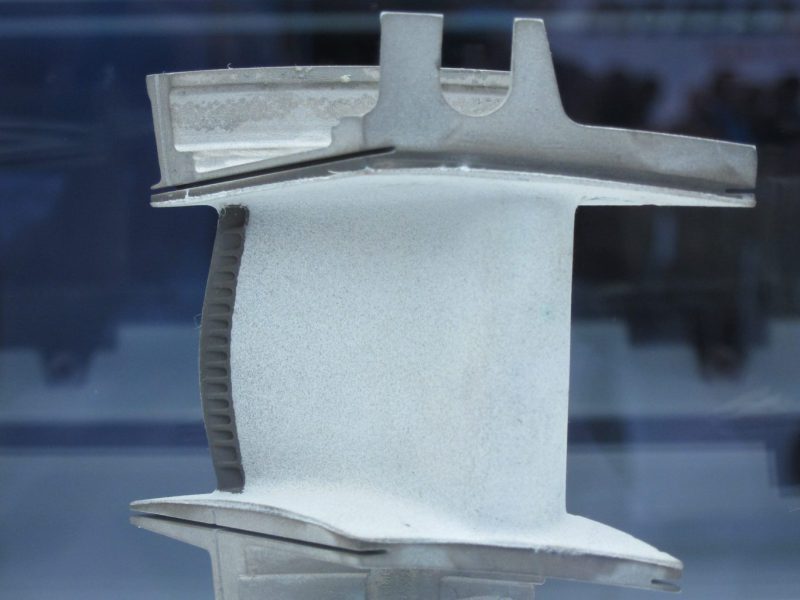
پوششهای سد حرارتی بر پایه زیرکونیا
پوششهای سد حرارتی
گروهی از پوششها به نام پوششهای سد حرارتی وجود دارند که وظیفه آنها کاهش دمای اجزا و در نتیجه افزایش طول عمر آنها است. در سالهای اخیر استفاده از فناوری نانو در تهیه پودرهای زیرکونیای پایدار شده با آلایندههای مختلف برای کاربرد در این پوششها، باعث بهبود چشمگیر در خواص مختلف این آنها از قبیل کاهش هدایت حرارتی، افزایش مقاومت به شوک حرارتی، افزایش استحکام چسبندگی پوشش به زیرلایه و بهبود خوردگی داغ این پوششها در مقایسه با پوششهای متداول شده است. این پوششها، ترکیبی از لایههای متعدد پوشش هستند که هر لایه دارای عملکرد و نیاز خاصی است به گونهای که لایه نهایی (فوقانی) به عنوان عایق حرارتی عموما از جنس زیرکونیای پایدار شده است.

تصویر میکروسکپی از ساختار پوششهای سد حرارتی
فواید پوششهای سد حرارتی
از پوششهای سد حرارتی در پرههای توربینها، تیغهها، پنلهای احتراق در موتورهای توربین گاز و عایق کردن استفاده میشود. کاهش دمای ناشی از وجود این نوع پوششها بهطور مستقیم در کاهش میزان اکسیداسیون پدیدار میشود. همچنین در اجزای دوار نیز مقدار آسیب ناشی از خزش به میزان قابل توجهی کاهش مییابد. با اعمال این پوششها بر روی زیرلایه این امکان فراهم میشود که آلیاژ زیرلایه بتواند درصد بیشتری از ویژگیهای ساختاری خود را در دمای اتاق حفظ کند. علاوهبراین هوای کمپرسور که برای خنک کردن قطعات استفاده میشود، ممکن است برای تولید نیروی رانش تغییر مسیر دهد و همین امر سبب میشود که راندمان موتورها افزایش یابد. تمام موارد ذکر شده نتیجه مستقیم ناشی از کاهش دمای این پوششها است که علاوه بر اینها فواید دیگری نیز وجود دارد که بهطور غیر مستقیم از این امر تاثیر میپذیرد. به عنوان مثال، پوششهای سد حرارتی با کاهش تغییرات موضعی دما، سبب کاهش اعوجاج و بهبود عمر خستگی حرارتی میشوند. از طرفی این پوششها انتقال دمای درون اجزا را تحت تاثیر قرار داده و با کاهش تغییر ناگهانی انرژی ورودی به اجزای دما بالا نظیر پرههای توربین هنگام صعود و فرود هواپیما و ایجاد هدایت حرارتی کمتر، بر عمر خستگی حرارتی اجزای فلزی تاثیر مثبت میگذارند.
خواص و مواد مورد نیاز در پوششهای سد حرارتی
برای انتخاب مواد مورد استفاده در این پوششها، باید ویژگیهای زیر در نظر گرفته شود:
- نقطه ذوب بالا
- هدایت حرارتی پایین
- ضریب انبساط حرارتی بالا و نزدیک به پوششهای فلزی
- مقاومت به اکسیداسیون بالا
- مقاومت به خوردگی نسبتا بالا
- مقاومت به کرنش بالا
- پایداری فازی مناسب
با توجه به ویژگیهای مذکور، در بین مواد سرامیکی مختلف، زیرکونیا میتواند انتخاب بسیار مناسبی باشد. از طرف دیگر زیرکونیای خالص به دلیل انتقالات فازی طی سرمایش و گرمایش، منجر به ایجاد ترک در این پوششها خواهد شد. بنابراین با افزودن عناصر نادر خاکی همچون Y2O3، MgO، CaO، CeO2، In2O3 و Sc2O3 فازهای استحالهناپذیر و پایدار زیرکونیا بهدست خواهد آمد که از این بین Y2O3 منجر به ایجاد فاز پایدار تتراگونال زیرکونیا خواهد شد و بیشترین کاربرد را در صنایع مختلف دارد.
در سالهاي اخیر ایجاد پوششهای سد حرارتی نانوساختار با استفاده از نانوپودرهاي گرانوله شده شده، موجب بهبود چشمگیر خواص این پوششها شده است. کاهش هـدایت حرارتی، افزایش استحکام چسبندگی پوشش به زیرلایه، افزایش تحمـل شـوكهاي حرارتـی، بهبـود خـواص مکانیکی و خورگی داغ پوشش سد حرارتی، از جمله مزایاي استفاده از نانوپودرها براي ایجاد پوششهـاي سـد حرارتی نانوساختار میباشد.
روشهای تولید نانوذرات زیرکونیای پایدار شده با ایتریا
خواص قطعات سرامیکی به عواملی چون اندازه ذرات، شکل ذرات، خلوص و یکنواختی پودر مصرفی بهطور مستقیم بستگی دارد و به واکنشهای حین پخت که خود متاثر از نوع و چگونگی مواد اولیه است نیز مربوط میشود. اندازه ذرات، شکل ذرات و خواص محصول نهایی از جمله عواملی هستند که میتوان با انتخاب روش تولید مناسب به کنترل دقیق آنها پرداخت. روشهاي متعددي براي تهیه اکسیدهاي فلزي نانومتري وجود دارد. براي ساخت نانوذرات زیرکونیایی خالص و یا آلاییده شده با عناصر مختلف، سه روش تولید در فاز جامد، مایع و گاز گزارش شده اسـت. روش فـاز جامـد شامل فرایندي طولانی بوده و محصول با گلولههاي آسیاب تولید میشود. روشهاي فاز گازي نیاز به تجهیـزات خاص و گران قیمت دارند. ولی روشهاي فاز مایع داراي مزایایی نظیر ارزان بـودن فراینـد تولیـد و یکنـواختی محصول تهیه شده میباشند که شامل روشهای متعددی نظیر هیدروترمال، سلژل، همرسوبی و … است.
ضخامت پوششهای سد حرارتی
کاهش دما متناسب با ضخامت پوشش است. بنابراین هر چه ضخامت پوشش بیشتر باشد، مطلوبتر است. بااینحال افزایش نامحدود ضخامت نیز به دلایل زیر مضر است:
- وزن اضافی به قطعه تحمیل میکند که برای اجزای دوار مانند پرههای توربین مضر است.
- افزایش ضخامت، مقدار تنش پسماند و انرژی کرنش کل را افزایش میدهد و پوشش سرامیکی را مستعد شکست میکند.
- هرچه لایه سرامیکی عایق ضخیمتر باشد، دمای سطح آن بالاتر میرود که منجر به امکان تفجوشی و مشکلات ساختاری و حرارتی مرتبط میشود.